Laboratories Must Start Exploiting the Benefits of Digitalization
As a tight labor market makes it difficult to find staff, and tougher economic conditions start to bite, laboratory managers are being forced to think hard about driving efficiency. Using the power of computer-based laboratory informatics solutions provides an easy win, but many organizations are still not fully exploiting the benefits that solutions such as LIMS offer. Reducing the number of manual ‘touch points’ and interventions for samples and their data is key to driving up efficiency.
Polling Provides Current Laboratory Status
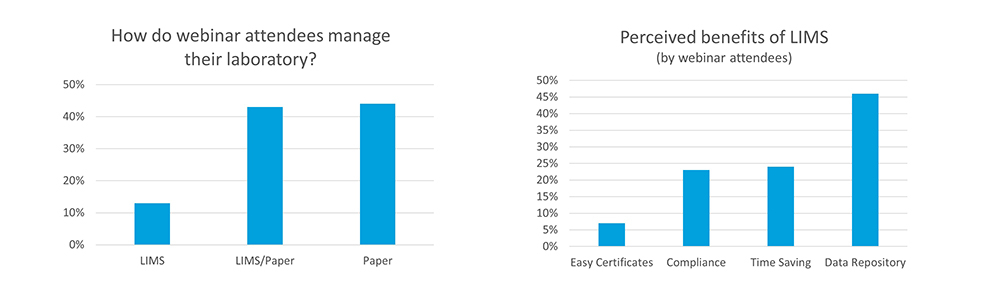
Autoscribe regularly hold educational webinars for the laboratory industry. From polling in these webinars it is clear that many laboratories have a lot more they can do to automate and streamline their processes. Our webinar ‘Utilizing LIMS to Take Your Laboratory Paperless’ had close to 500 attendees. Our polling questions to this audience included:
What do attendees use to manage their lab data?
- We have a LIMS (13% of respondents)
- We have a LIMS but still need to use paper (43% of respondents)
- We use paper or spreadsheets (44% of respondents)
What do attendees see as the benefits of a LIMS?
- Automatic creation of Certificates of Analysis (7% of respondents)
- Compliance with regulatory requirements (23% of respondents)
- Free up laboratory staff time (24% of respondents)
- Keep all data in one place (46% of respondents)
In our webinar on ‘Incorporating ISO 17025 into your laboratory’, with around 400 attendees, the following polling questions were asked:
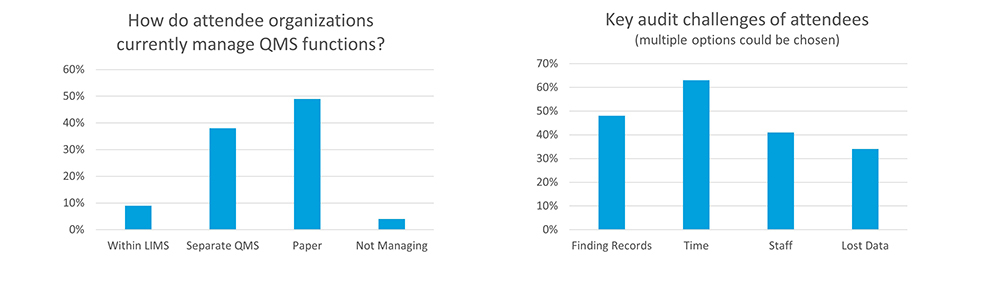
How is your organization currently managing controlled documents, employee training documentation and issue management or corrective action preventive actions (CAPA)?
- Integrated in our LIMS (9% of respondents)
- Separate QMS electronic system (38% of respondents)
- Spreadsheets or paper based (49% of respondents)
- Not managing these (4% of respondents)
What are the most significant audit challenges for your organization (multiple options could be chosen, and not all responded)?
- Too many places to look for records selected (chosen by 48% of respondents)
- Time required to compile records (chosen by 63% of respondents)
- Availability of staff to assist auditor in reviewing records (chosen by 41% of respondents)
- Lost/incomplete records (chosen by 34% of respondents)
Stuck in a Dysfunctional World
Even though not all attendees respond to every question, the size of the poll provides interesting insight into the state of digitalization within the laboratory. Observations include:
- Paper records
The use of paper records or spreadsheets (maybe also with a LIMS) is still common. In the first webinar nearly half of all respondents did not have a LIMS at all, while a good proportion said they have a LIMS but use paper as well. It shows many labs have a way to go even on the first basic steps to digitalization.- To those lab managers looking to justify the purchase of a LIMS for their lab we would recommend this white paper as a source of inspiration.
- Reasons for a LIMS
One of the main reasons for using a LIMS is keeping all the data in one place. If you have endless cabinets with laboratory notebooks containing test results you will know how difficult it can be to pull data for a certificate of analysis, customer audit or management report. But case studies show many other reasons for using a LIMS:- Faster sample registration and Instrument Integration
A lubricants company that, among other sample types, tests field samples provided by customers replaced a hybrid paper and electronic system and, each day, reduced the time it took a technician to register samples from 5-6 hours to one hour. By integrating their instruments with LIMS and introducing other automation to replace paper-based steps, the number of manual touch points for each sample was reduced from around 11 to 3-4, with an associated reduction in transcription errors and improvement in turn-around time. Finally, having electronic records makes it simple to compare original batch results against results from field samples to see if there has been significant degradation of the product. - Rapid creation of Certificates of Analysis and Integration with other systems
Similarly, a rapidly growing UK based specialist testing company needed to replace an existing hybrid paper and Microsoft Access system. As well as improving the sample management workflow and recording of results, the previously manual and time-consuming processes of creating certificates of analysis, customer quotes and invoices as well as the transfer of those invoice to a finance system were automated. Having all the information in a single system also means that required data is instantly available for reporting and audit purposes. - Keeping production moving
In a specialty chemical company, whose products include pharmaceutical APIs, a paper-based result approval process took 2-3 hours to complete, with reactors idle while it was completed. The approval process was digitized, and reactors now rarely stand idle waiting for result approval. This resulted in a significant improvement to production efficiency and company profitability. - Automation leads to higher efficiency
Other examples include a veterinary testing lab that saved 2-3 hours per employee per day during their peak season through improved digitalization of the laboratory, and a manufacturing organization where the time to create lot traceability reports in response to customer complaints was reduced from up to two days using the previous paper-based system to a matter of seconds using an integrated LIMS solution.
- Faster sample registration and Instrument Integration
- Lack of Integration to QMS and Other Systems
Only 9% of respondents said that their LIMS and QMS were integrated into a single system. This is an area that has the potential to provide many benefits, for example linking training records to LIMS functions to check, in real time, that staff have the correct training to complete the task, or linking CAPA directly to sample or batch records within LIMS. The lesson here is to look for ways of integrating, or at least linking your systems:- Think about integrating instrument maintenance records, staff training, and documentation such as operational procedures within the LIMS
- Be aware of manual interfaces between the LIMS and external systems, either instruments used within the lab, or finance and resource planning systems, and integrate them when you can
Summary
The benefits of digitalization have been outlined many times, but what may be missing for many is evidence of these benefits. With a large number of case studies from Autoscribe’s customers we can provide insights into the benefits that other organizations have gained from digitalization of the laboratory environment.
The key is to drive your laboratory to make the first small steps into LIMS and then constantly look at integrating your internal systems to drive efficiency. With the current pressure on businesses everywhere to do more with less is an easy win you cannot afford not to ignore.